NCN, progettazione stampi per elastomeri
What we do
Design and manufacturing of elastomer molds
Founded in 2013, NCN Technology has always strived to supply customers with the design and manufacturing of elastomer molds, also providing professional consulting services for industrial gaskets manufacturers throughout the project. With more than 20 years’ experience in the field, our committed search for tailor-made solutions in mold making and development is what really makes our company stand out.
To reach our goals in mold design, we employ cutting-edge 2D- and 3D CAD software.
Furthermore, thanks to the collaboration with the best Italian mold making companies – located in the so-called “Sebino Rubber District”, we can provide our customers with full service: evaluation of the item to be created, mold design, manufacturing and delivery of the mold, ready to use and equipped with cold runner block.
In 2018 NCN Technology obtained the ISO 9001:2015 Quality management system certification .
To reach our goals in mold design, we employ cutting-edge 2D- and 3D CAD software.
Products and services
- Consulting for the items to be molded
- Consulting for mold design
- Mold design
- Mold manufacturing
- Mold supply and testing
- Product co-design in collaboration with the Customer
- After-sales consulting services and training on the best practices to follow for the use, assembly/disassembly and maintenance of the mold
Mission
Elastomer mold design and manufacturing is not a mere question of creating turnkey products: it is being committed to the development of efficient workflow, in order to minimize any possible drawback throughout the project, so as to save material and maximize the production process – in full automation – while improving the quality of the finished product itself. Therefore, our mission is to help companies create quality products, minimizing both costs and time, giving them the opportunity to compete in an ever-growing market.
How do we do it? Experience taught us that compounds are not all the same. For instance, when designing a mold, it is essential to know the idiosyncrasies of the material to be molded, being able to evaluate handling and parting lines, identify the right steel and thermal treatment to use (not to mention surface coatings), in order to improve the product’s performance and durability.
Elastomer mold design
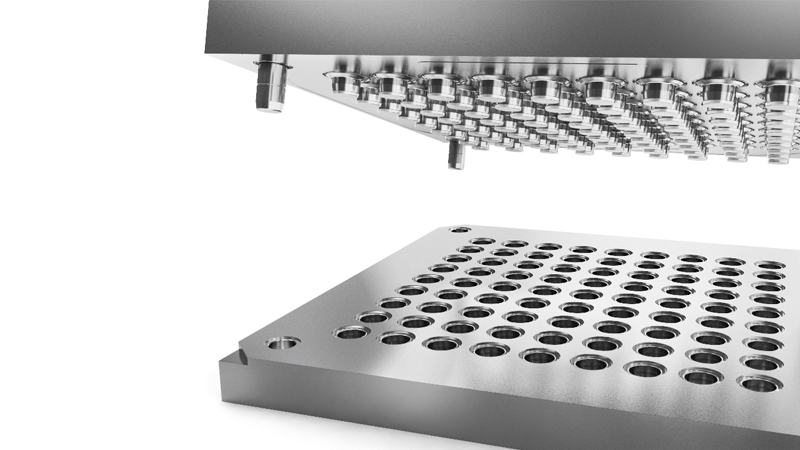
Compression molds
- Pilot molds for sampling
- Small-scale production
- Special materials
- Shot deburring by punching/cutting tools
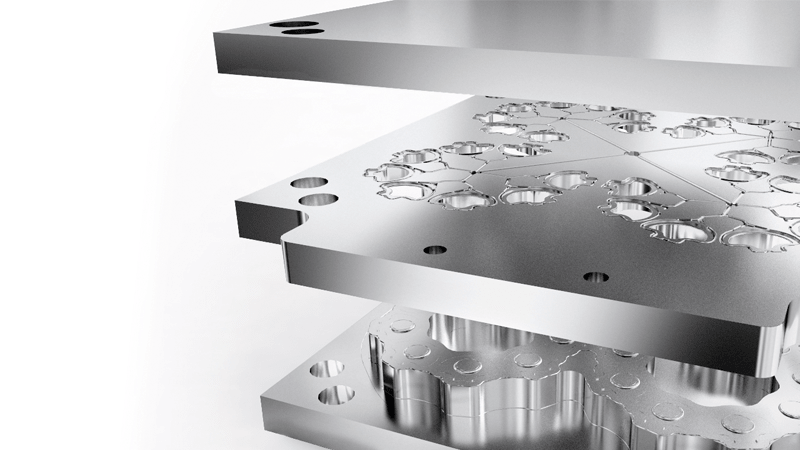
Injection molds
- Small-, medium- and large-scale production
- Equipped with single nozzle or multiple nozzles
- Automatic operation (unattended) – if applicable
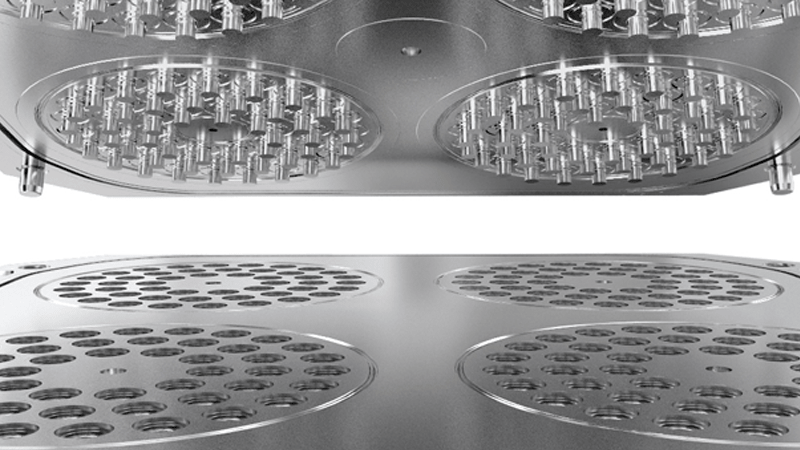
Injection-compression molds
- Small-, medium- and large-scale production
- Equipped with single nozzle or multiple nozzles
- Automatic operation – if applicable
- Shot deburring by punching/cutting tools
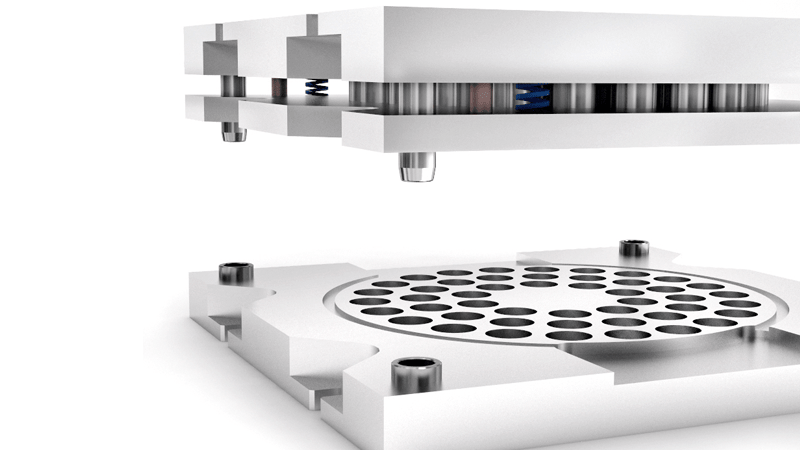
Punching/cutting tools
- Especially suitable for injection-compression and compression molds
- Medium. and large.scale production
- Pieces with constant burr on all cavities
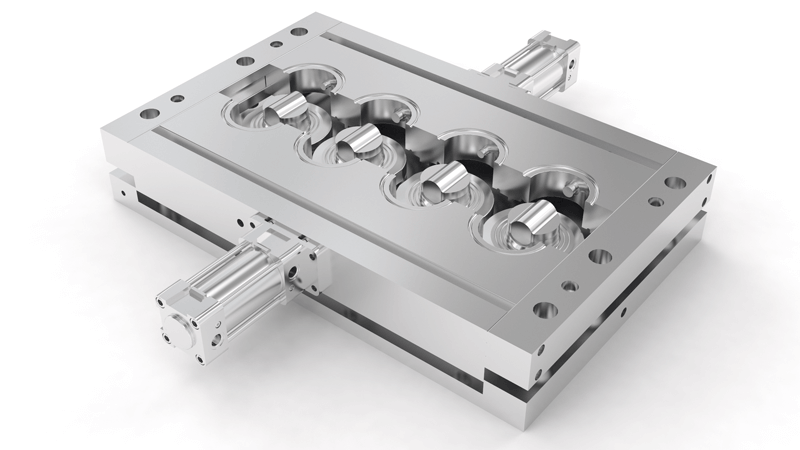
Special molds
- Complex geometry
- Combined movements with more than three plates, side-plates, sliding cores and retaining plates
- Single- and multiple nozzle injection or compression molding
- Tailor-made solutions
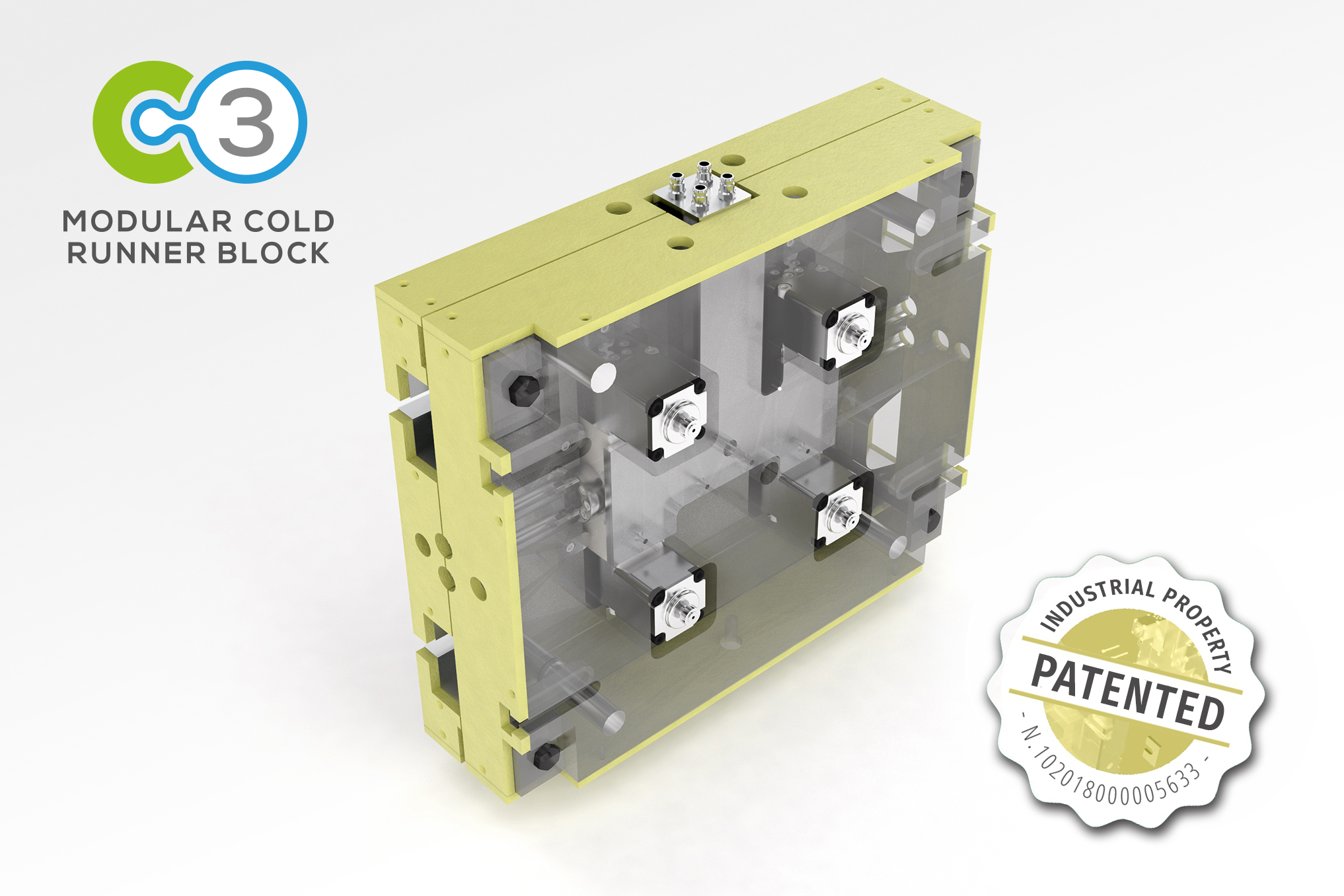
C3 Module
C³ is an innovative, modular cold runner block: simple, versatile and light. It allows for a reduction in costs both during the purchasing process and during use and maintenance.
Main pros:
- Quick compound change (about 20 min.) thanks to its interchangeable core.
- Easy and thorough cleaning of the core by means of special dowels.
- Full compatibility with all kind of forming presses, as it has no electrical connections.
- No risk of electrical failure, as the pre-existing heating plate on the press is used instead.
- Easy maintenance thanks to its modular structure.
- Temperature homogeneity of the plate in contact with the mold (thermal differential 2°C).
- Less stressed cooling units, because thermoregulation occurs only where the compound flows.
- Parallel nozzle cooling, so that nozzles always have the same temperature with each other.
- Low thickness and weight: a C3 of 570×470 cm weighs 300kg, with only 166mm in thickness, so as to allow greater opening of the press.
Discover all the benefits of cold runner C3, visit now
Research and Development
Due to its production rhythms and logic, the rubber industry generally tends to pay too little attention to R&D activities, which are fundamental to the innovation of production processes.
Here at NCN Technology ‘Research and Development’ is paramount. This means knowing a priori the needs of both our customers and the global market, to study and develop innovative solutions, regardless of requests of order.